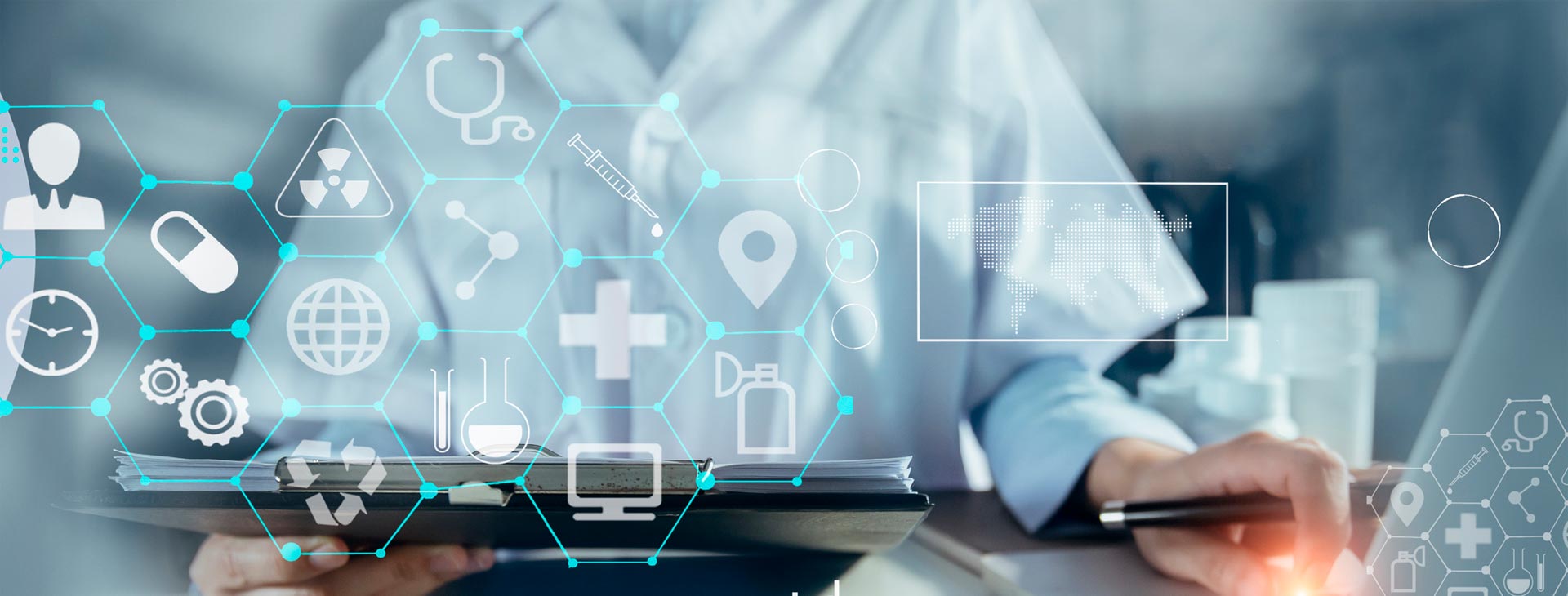
Sterval
Goodbye Paper, Hello Efficiency
As a leading provider of decontamination solutions for the healthcare industry, Sterval supplies disinfection and sterilisation machines to CSSDs across Ireland.
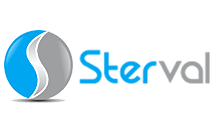
Client: | Sterval |
System Components: | Cellular & Wi-Fi connectivity, network provider, cloud service and browser-based dashboard access |
Sample End User: | NHS Imperial Trust, London |
The Challenge
Working with clients in a wide range of hospitals over many years, Sterval observed the burden that paper-based systems placed on CSSD managers and their teams when handling machine cycle reports.
Up to that point, Sterval’s machines had produced a printed report at the end of each cycle, but printer issues, laborious filing and time-consuming record retrieval impacted on the productivity and efficiency of CSSDs. Likewise, mislaid documentation and unsigned reports led to unnecessary downtime and exposed hospitals to legal action.
Looking for a solution that would streamline processes for its customers and add functionality to its machines, Sterval turned to us.
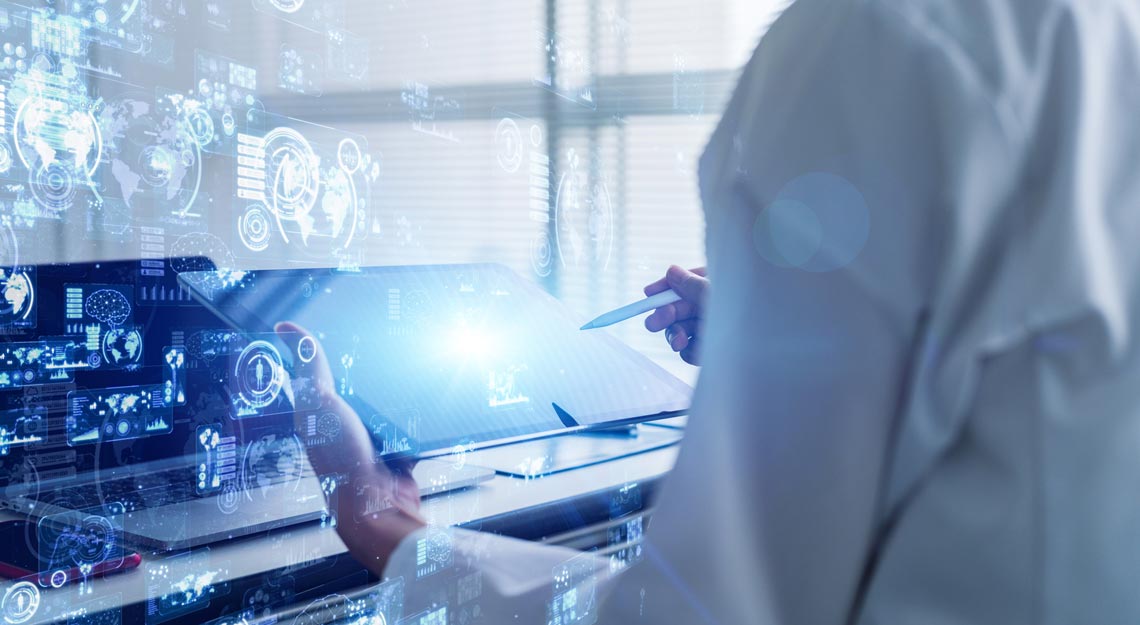
The Solution
In response, we integrated our innovative medical monitoring system – SteriSight – with Sterval’s line of autoclaves, instrument washers, washer disinfectors and ultrasonic cleaners to create a seamless solution that generates digital reports instead of paper ones.
No longer reliant on printouts, CSSD teams are now able to review, approve and securely archive all their machine cycle reports from an online dashboard. Managers can check on progress at any time throughout the day, and historical files can be retrieved at the touch of a button.
With hassle-free implementation, both new and existing Sterval customers have easily connected to SteriSight. Peace of mind is guaranteed as the system runs independently of the hospital network, so there is no interference with IT or data security.
The Results
Sterval’s customers saw the benefits as soon as SteriSight was introduced. By removing paper from the CSSD, administration has been considerably reduced, huge time and cost savings have been achieved and compliance has greatly increased.
Printer issues are now a thing of the past, meaning unnecessary downtime is avoided and delays to surgery are minimised. With automatic and secure online archiving, all machine reports are safely filed away, physical storage space is not required and traceability is guaranteed.
As reports can be retrieved immediately, resources are now freed up for more productive tasks. And, especially pleasing for CSSD managers, the easy-to-use dashboard makes staff training simple and quick.
System Highlights
- Elimination of paperwork, reduced administration and less downtime.
- More efficient processing and fewer delays to surgery.
- Independent, tamper-proof storage of machine cycle reports.
- Enhanced compliance and more protection against legal action.
- Instant file retrieval with secure online archiving.